Antistatic Biodegradable Films: Chiang Mai University Researchers Use Advent Metal Wires in Cutting-Edge Study
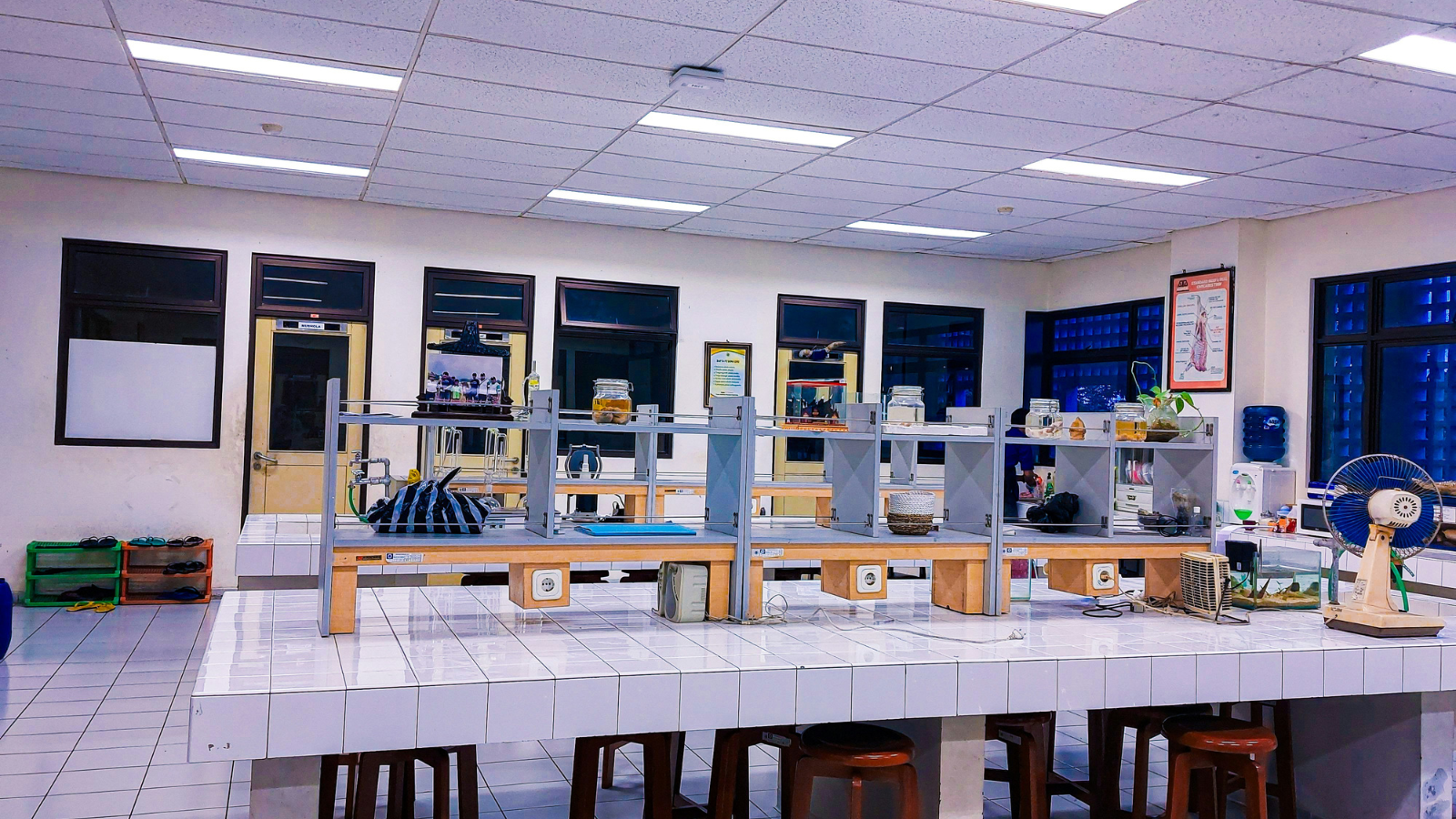-(5).png?width=50)
The environmental damage caused by plastic waste has intensified demand for biodegradable alternatives—especially in sectors like electronics, automotive, and consumer packaging.
Yet many bio-based polymers, while promising, face limitations: they can be flammable, lack antistatic properties, or underperform mechanically.
To address this, researchers from Chiang Mai University (Thailand) and Sungkyunkwan University (Republic of Korea) developed a new biodegradable composite that offers improved flame resistance, water resistance, and antistatic performance.
Their work was recently published in Polymers (June 2025) in a peer-reviewed article titled Flame Retardance and Antistatic Polybutylene Succinate/Polybutylene Adipate-Co-Terephthalate/Magnesium Composite [Rachtanapun et al., 2025].
Their composite is based on a blend of polybutylene succinate (PBS), polybutylene adipate-co-terephthalate (PBAT), epoxy resin, and magnesium oxide (MgO)—engineered using a melt blending process, then formed into films using twin-screw extrusion and film-blowing equipment.
To improve the electrical surface properties, the researchers tested two advanced surface treatments:
- Plasma sputtering using metal nanoparticles
- Sparking with metal wires to generate nano-metal particles directly on the film surface
For the sparking process, the team used titanium, copper, and aluminum wires (0.5 mm diameter) supplied by Advent Research Materials (Oxford, UK)—selected for their quality and suitability for scientific application:
“Ti, Cu, and Al wires (0.5 mm diameter) were purchased from Advent Research Materials Co., Ltd. (Oxford, UK).” (Rachtanapun et al., 2025)
Key Research Outcomes
The most successful composite formulation—PBS/E1/PBAT with 15% MgO—achieved a UL-94 V-1 flame retardancy rating, with no flaming drips during testing. Mechanical performance also improved, with elongation at break increasing to over 500%, attributed to the compatibility-enhancing role of the epoxy resin and dispersion of MgO particles.
- Mechanical enhancement: Epoxy improved compatibility between PBS and PBAT, raising tensile strength from 19 MPa to 25 MPa.
- Flame retardancy: The MgO-filled composite achieved a UL-94 V-1 rating, indicating improved flame resistance.
- Antistatic performance: Plasma sputtering produced the best results overall, but the sparking process using Advent wires showed meaningful reductions in static charge, offering a low-cost and scalable alternative for surface treatment.
In terms of antistatic performance:
- Plasma sputtering achieved the greatest reduction in surface voltage, down to as low as 0.036 kV
- Sparking with Advent wires also led to substantial improvements, reducing surface charge from 1.56 kV (untreated) to as low as 0.364 kV
This positions the material as a strong candidate for sustainable packaging in electronics, where static dissipation and flame resistance are critical.
Real-World Potential
The combination of improved flame retardancy and antistatic behaviour makes these biodegradable composites suitable for packaging sensitive electronic components, reducing reliance on petroleum-based insulators.
As industries look for high-performance, biodegradable alternatives to petroleum-based plastics, this study demonstrates that it is possible to meet both environmental and functional requirements.
The study contributes to growing efforts to design sustainable functional materials for industrial use, while demonstrating how access to reliable research-grade materials—such as those supplied by Advent—supports innovation across global academic labs.
Reference
Rachtanapun, P., Suhr, J., Oh, E., Thajai, N., Kanthiya, T., Kiattipornpithak, K., et al. (2025). Flame Retardance and Antistatic Polybutylene Succinate/Polybutylene Adipate-Co-Terephthalate/Magnesium Composite. Polymers, 17(12), 1675. https://doi.org/10.3390/polym17121675